Civata somunlar, birçok uygulamada sıklıkla kullanılan bağlantı elemanlarıdır. Ancak, zaman içinde çeşitli problemlerle karşılaşabilirler. Bu makalede civata somunların sıkça karşılaşılan problemlerini ve bunların çözümlerini ele alacağız.
1. Gevşeme Problemi:
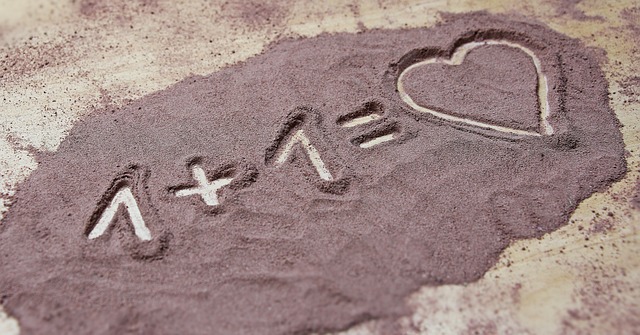
Civata somunlar zamanla gevşeyebilir, özellikle titreşimli ortamlarda veya sürekli hareket eden parçalarda. Bu durum, bağlantının güvenliğini tehlikeye atar. Gevşeme probleminin önlenmesi için kilitleme elemanları kullanılabilir. Örneğin, somun kilitleri veya elastic stop somunları bu sorunu çözebilir. Bu tür kilitleme mekanizmaları, somunun istenmeyen gevşemeye karşı tutunmasını sağlar.
2. Oksidasyon Problemi:
Civata somunlar, zamanla oksidasyona maruz kalabilir. Bu durum, somunların gevşemesine veya paslanmasına neden olabilir. Oksidasyon problemini önlemek için, paslanmaz çelik veya galvanizli somunlar tercih edilebilir. Ayrıca, düzenli bakım ve temizleme işlemleri de somunların ömrünü uzatabilir.
3. Kırılma Problemi:
Yoğun gerilmelere veya yanlış montaj tekniklerine maruz kalan civata somunlar kırılabilir. Bu durum, bağlantının güvenliğini tehlikeye atar ve hasara neden olabilir. Kırılma problemini en aza indirmek için doğru sıkma torku kullanılmalı ve somunların uygun mukavemet değerlerine sahip olması sağlanmalıdır. Ayrıca, yüksek kaliteli malzemelerden üretilmiş somunlar tercih edilmelidir.
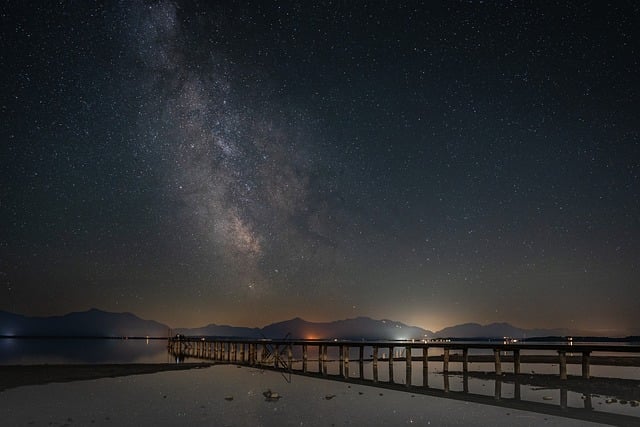
4. Kayma Problemi:
Bazı durumlarda, civata somunlar yerinde sıkılı kalmaz ve kayar. Bu sorun, bağlantının güvenliğini azaltır. Kayma problemini önlemek için somun altına rondela veya dişli kilitleme elemanları eklenerek daha iyi bir tutuş sağlanabilir.
5. Bozulma Problemi:
Uzun süreli kullanım veya yanlış montaj sonucunda civata somunların dişleri bozulabilir. Bozulma problemini önlemek için doğru sıkma tekniği kullanılmalı ve somunlar düzenli olarak kontrol edilmelidir. Gerekirse, bozulan somunlar değiştirilmelidir.
Civata somunların sıklıkla karşılaşılan bu problemleri, uygun önlemler alınarak çözülebilir. Doğru montaj tekniklerine uyulması, uygun kilitleme mekanizmalarının kullanılması ve düzenli bakım işlemlerinin yapılması, somunların sağlam ve güvenli bir şekilde çalışmasını sağlar. Bu sayede, bağlantı elemanlarından beklenen performans elde edilebilir.
Yanlış somun ve civata eşleştirmesi
Yanlış somun ve civata eşleştirmesi, birçok inşaat veya montaj uygulamasında karşılaşılan yaygın bir sorundur. Bu hatalı eşleştirme, uyumsuz parçaların kullanılması nedeniyle birçok olumsuz sonuca yol açabilir. Hem zaman hem de maliyet açısından ciddi sorunlar ortaya çıkabilir ve hatta güvenlik riskleri meydana gelebilir.
Bu sorunun temel nedenlerinden biri, farklı ölçü sistemleri veya standartların kullanılmasıdır. Örneğin, metrik ve imperial (inç) sistemleri arasındaki farklar, doğru parçaların seçilmesini zorlaştırabilir. Ayrıca, malzeme türüne, diş sayısına veya yüzey işlemine dikkat etmeden parçaların rastgele bir şekilde birleştirilmesi de yanlış somun ve civata eşleştirmesine yol açabilir.
Bu hatalı eşleştirme sonucunda ortaya çıkan bazı sorunlar şunlardır: gevşeme, sızdırma, kaçak, dayanıksızlık ve parça bozulması gibi durumlar. Örneğin, uyumsuz bir somun ve civata birleşimi, bağlantının zamanla gevşemesine ve nihayetinde ayrılmasına neden olabilir. Bunun sonucunda, montaj yapılan parçaların performansı azalır ve işlevselliği olumsuz etkilenir.
Bu sorunların önlenmesi için doğru somun ve civata eşleştirmesinin yapılması çok önemlidir. Bu, öncelikle parçaların doğru ölçü sistemi veya standarta göre seçilmesini gerektirir. Her malzeme türüne ve uygulamaya uygun olan somun ve civataların kullanılması da büyük bir önem taşır. Ayrıca, bağlantının istenen dayanıklılığa ve güvenliğe sahip olmasını sağlamak için doğru diş sayısı ve yüzey işlemi seçilmelidir.
Sonuç olarak, yanlış somun ve civata eşleştirmesi ciddi sorunlara yol açabilir. Doğru parçaların seçimi ve uygun montaj tekniklerinin kullanılması, bu sorunu önlemek için kritik öneme sahiptir. İnşaat veya montaj sürecinde her zaman doğru somun ve civata eşleştirmelerine dikkat etmek, zamandan ve maliyetten tasarruf etmenin yanı sıra güvenliği de sağlamak anlamına gelir.
Boyut uyumsuzlukları ve tolerans sorunları
Boyut uyumsuzlukları ve tolerans sorunları, birçok endüstriyel süreçte karşılaşılan önemli meselelerdir. Üretimdeki hassas ölçümler ve bileşenler arasındaki uyum, bir ürünün kalitesini etkileyebilir ve sonuçta müşteri memnuniyetini azaltabilir.
Boyut uyumsuzlukları, tasarım aşamasında belirlenen ölçülerin gerçek üretim sonuçlarıyla uyuşmaması durumudur. Tasarımcılar, bir parçanın belirli boyutlarına tolerans değerleri atarlar. Ancak, üretim sürecinde malzeme özellikleri, işleme hataları veya diğer faktörler nedeniyle bu tolerans değerleri aşılabilmektedir. Bu durumda, parçalar birbiriyle uyumsuz hale gelebilir ve montaj süreci zorlaşabilir. Ayrıca, boyut uyumsuzlukları ürünün performansını ve dayanıklılığını da olumsuz etkileyebilir.
Tolerans sorunları ise bir parçanın belirli bir tolerans aralığında üretilmesine rağmen, kullanım sırasında istenmeyen sonuçlara yol açabilecek sapmalardır. Örneğin, bir makinede bir milin yatağına tam olarak oturmaması veya bir vida ile somunun gevşek olması gibi durumlar tolerans sorunlarına örnek olarak verilebilir. Bu tür sorunlar, ürünün çalışma kalitesini düşürebilir ve hatta güvenlik riski oluşturabilir.
Boyut uyumsuzlukları ve tolerans sorunlarıyla başa çıkmak için öncelikle tasarım aşamasında doğru tolerans değerleri belirlenmelidir. İmalat sürecinde kalite kontrol önlemleri alınmalı ve uygun hassasiyetle parçalar üretilmelidir. Ayrıca, montaj aşamasında da dikkatli bir şekilde uyum kontrolü yapılmalıdır. Gelişmiş teknolojiler ve otomasyon sistemleri, boyut uyumsuzluklarını ve tolerans sorunlarını azaltmaya yardımcı olabilir.
Sonuç olarak, boyut uyumsuzlukları ve tolerans sorunları, üretim süreçlerinde dikkate alınması gereken kritik faktörlerdir. Doğru tasarım, kalite kontrol ve montaj yöntemleri kullanarak bu sorunların önüne geçilebilir ve yüksek kaliteli ürünler elde edilebilir.
Zor erişim noktalarında montaj zorlukları
Zor erişim noktalarında montaj zorlukları, birçok endüstride karşılaşılan yaygın bir sorundur. Bu noktalarda ekipman veya yapıların kurulumu veya montajı, fiziksel kısıtlamalar nedeniyle zorlu bir görev olabilir. Bu makalede, zor erişim noktalarında montaj sürecinde ortaya çıkan zorluklara odaklanacağız.
Zor erişim noktaları, dar alanlar, yükseklikler veya karmaşık yapılardan kaynaklanabilir. Örneğin, bina dışındaki bir antenin montajı ya da köprü altındaki bir borunun onarımı gibi durumlar söz konusu olabilir. Bu tür projelerde çalışanlar, sınırlı alan, güvenlik riskleri ve zaman baskısı gibi zorluklarla karşılaşabilir.
Montaj sürecindeki en büyük engellerden biri, erişilebilirliğin sınırlı olmasıdır. Dar geçitler veya yükseklikler, personelin malzemeleri taşımasını veya işleri yapmasını zorlaştırabilir. Ayrıca, doğru ekipmanın seçimi ve kullanımı da önemlidir. Özellikle yüksek irtifalarda veya tehlikeli alanlarda çalışırken, işçilerin güvenliği için uygun ekipman sağlanmalıdır.
Bu tür montaj işlemlerinde planlama ve koordinasyon da hayati önem taşır. İşçilerin zamanlarını ve kaynaklarını etkin bir şekilde yönetmeleri gerekir. Ayrıca, işçilerin eğitimli ve deneyimli olması da zorluğun üstesinden gelmede yardımcı olabilir. Gerekli becerilere sahip personel, karmaşık montaj süreçlerini daha kolay yönetebilir.
Sonuç olarak, zor erişim noktalarında montaj zorlukları, çeşitli endüstrilerde karşılaşılan bir gerçektir. Bu zorlukların üstesinden gelmek için doğru planlama, uygun ekipman kullanımı ve eğitimli personel önemlidir. İş güvenliği de göz ardı edilmemeli ve her zaman öncelikli olmalıdır. Ekipman kurulumu veya montajıyla uğraşan herkes, bu zorlukları dikkate almalı ve gerekli önlemleri almalıdır.
Çatlak ve kırık somunlar
Çatlak ve kırık somunlar, birçok endüstriyel sektörde sıkça karşılaşılan bir sorundur. Bu somunların doğru şekilde kullanılmaması veya aşırı stres altında kalması sonucunda çatlamalar ve kırılmalar meydana gelebilir. Bu durum, ekipmanların güvenliği, sürekliliği ve performansı açısından ciddi bir risk oluşturabilir.
Öncelikle, çatlak ve kırık somunların neden meydana geldiğini anlamak önemlidir. Genellikle yanlış montaj veya düşük kaliteli malzeme kullanımı bu sorunlara yol açar. Somunların yeterli sıkılıkta olmaması, titreşimler, darbeler veya aşırı yüklemeler de çatlaklara ve kırılmalara neden olabilir. Bunun yanı sıra, somunların yaşlanması veya aşınması da bu sorunlara katkıda bulunabilir.
Bu tür sorunların etkileri ihmal edilemez. Çatlak ve kırık somunlar, ekipmanların tutarlılığını ve güvenilirliğini azaltabilir. Ayrıca, sürekli olmayan sıkıntılar nedeniyle beklenmeyen arızaların ortaya çıkma olasılığı artar. Bu durum da üretkenlik kayıplarına, maliyet artışlarına ve hatta ciddi kazalara yol açabilir.
Bu sorunu çözmek için önleyici tedbirler almak önemlidir. İlk olarak, yüksek kaliteli somunlar kullanılmalı ve doğru montaj prosedürleri takip edilmelidir. Somunların yeterli sıkılıkta olması sağlanmalı ve düzenli olarak kontrol edilmelidir. Ayrıca, titreşim emici contalar veya kilitleme elemanları gibi ilave önlemler almak da faydalı olabilir.
Sonuç olarak, çatlak ve kırık somunlar endüstriyel sektörlerde ciddi bir sorundur. Bu sorunların etkilerini azaltmak için kaliteli malzeme kullanımı, doğru montaj ve düzenli bakım gereklidir. Somunlar düzgün bir şekilde kullanıldığında ve sürekli olarak kontrol edildiğinde, ekipman güvenliği ve performansı artar, üretkenlik kayıpları ve beklenmedik arızalar azalır.
Yüksek sıcaklıkta somunların performansı
Yüksek sıcaklıklar, birçok endüstriyel ortamda yaygın olarak karşılaşılan bir durumdur ve bu durum somunların performansını etkileyebilir. Somunlar, bağlantı elemanları olarak kullanıldıklarında, sıcaklık değişiklikleri nedeniyle gevşeme veya deformasyon gibi sorunlarla karşılaşabilirler. Bu nedenle, yüksek sıcaklıkta çalışan uygulamalarda somun seçimi ve doğru montaj teknikleri büyük önem taşır.
Yüksek sıcaklık ortamlarında çalışan somunların performansını etkileyen bir faktör, malzeme seçimidir. Genellikle, alaşımlı çelik somunlar, yüksek sıcaklıklara dayanıklılık sağlamak için tercih edilir. Bu somunlar, oksidasyona ve termal genleşmeye karşı direnç gösterir. Ayrıca, paslanmaz çelik somunlar da yüksek sıcaklıkta iyi performans sergileyebilir.
Somunların yüksek sıcaklıkta optimal performans göstermesi için doğru montaj teknikleri kullanılmalıdır. Öncelikle, somunlar yeterli sıkılıkta olmalıdır, ancak aşırı sıkıştırmaktan kaçınılmalıdır. Aşırı sıkıştırma, somunun deformasyona uğramasına veya gevşemesine neden olabilir. İkinci olarak, sıcaklık değişiklikleri sırasında somunların genleşme ve büzülme yapabilmesi için yeterli boşluk bırakılmalıdır. Bu, termal stresin azaltılmasına yardımcı olur.
Yüksek sıcaklıkta somunların performansını artırmak için bir diğer önemli faktör, uygun yağlama ve contaların kullanılmasıdır. Yüksek sıcaklık ortamlarında çalışan somunlar için özel yağlama maddeleri ve yüksek sıcaklığa dayanıklı conta malzemeleri mevcuttur. Bu malzemeler, sürtünmeyi azaltarak ve sızdırmazlık sağlayarak somunların daha iyi performans göstermesini sağlar.
Sonuç olarak, yüksek sıcaklıkta çalışan somunların performansını etkileyen birçok faktör vardır. Malzeme seçimi, doğru montaj teknikleri, uygun yağlama ve contalar gibi unsurlar, somunların yüksek sıcaklık ortamlarında güvenilir bir şekilde çalışmasını sağlar. Bu nedenle, endüstriyel uygulamalarda yüksek sıcaklıkla karşılaşılan durumlarda, doğru somun seçimine ve doğru montaj yöntemlerine dikkat edilmelidir.
Montaj hataları ve yanlış sıkma yöntemleri
Montaj süreci, bir ürünün doğru şekilde kurulumunu sağlayan önemli bir adımdır. Ancak, montaj esnasında yapılan hatalar ve yanlış sıkma yöntemleri, ürünün performansını olumsuz etkileyebilir ve potansiyel güvenlik riskleri oluşturabilir. Bu makalede, montaj hataları ve yanlış sıkma yöntemlerine odaklanarak, bu sorunların nasıl önlenebileceğini inceleyeceğiz.
Birinci hata, montaj işlemine yeterli zaman ayırmamaktır. Aceleyle yapılan montajlar, dikkatsizliklere sebep olabilir ve gözden kaçabilecek ayrıntıları beraberinde getirir. Montajın her aşamasına gereken özenin gösterilmesi önemlidir. Montaj talimatlarına uygun hareket edilmeli ve gerekli adımlar atlanmamalıdır.
İkinci hata, yanlış sıkma yöntemlerinin kullanılmasıdır. İdeal sıkma kuvveti, ürünün tasarımına ve kullanım amacına bağlı olarak belirlenmelidir. Çok az veya çok fazla sıkma kuvveti, ürünün işlevselliğini bozabilir veya bileşenlerin zarar görmesine neden olabilir. Bu nedenle, montaj sırasında doğru sıkma yöntemleri ve araçları kullanılmalıdır.
Üçüncü hata, uygun olmayan montaj malzemelerinin kullanılmasıdır. Kalitesiz vidalar, cıvatalar veya diğer bağlantı elemanları, montajın güvenilirliğini azaltabilir. Montaj malzemelerinin doğru özelliklere sahip olduğundan emin olunmalı ve üretici tarafından önerilen standartlara uygun seçilmelidir.
Dördüncü hata, montaj talimatlarının göz ardı edilmesidir. Ürünle birlikte gelen montaj talimatları, doğru kurulum için vazgeçilmez bir kaynaktır. Talimatların dikkatlice okunması ve adımların takip edilmesi gerekmektedir. Montaj sürecinde herhangi bir belirsizlik varsa, üretici veya uzmana başvurulmalıdır.
Son olarak, beceriksiz veya yeterince eğitimli olmayan personel tarafından yapılan montaj, büyük sorunlara yol açabilir. Montaj işlemlerinin, tecrübeli ve bilgili kişiler tarafından gerçekleştirilmesi önemlidir. Eğitimli personel, hataları en aza indirecek ve ürünün doğru şekilde monte edilmesini sağlayacaktır.
Montaj sürecinde yapılan hatalar ve yanlış sıkma yöntemleri, ürünün güvenilirliğini etkiler ve pahalı tamir veya yeniden montaj işlemlerine neden olabilir. Bu nedenle, montaj sürecinde dikkatli olmak, doğru sıkma yöntemlerini kullanmak ve talimatlara uymak önemlidir. Doğru montaj, ürünün uzun ömürlü olmasını sağlar ve güvenli bir şekilde kullanılmasına yardımcı olur.